Business
Precision and Efficiency: Laser-Based Solutions for Additive Manufacturing
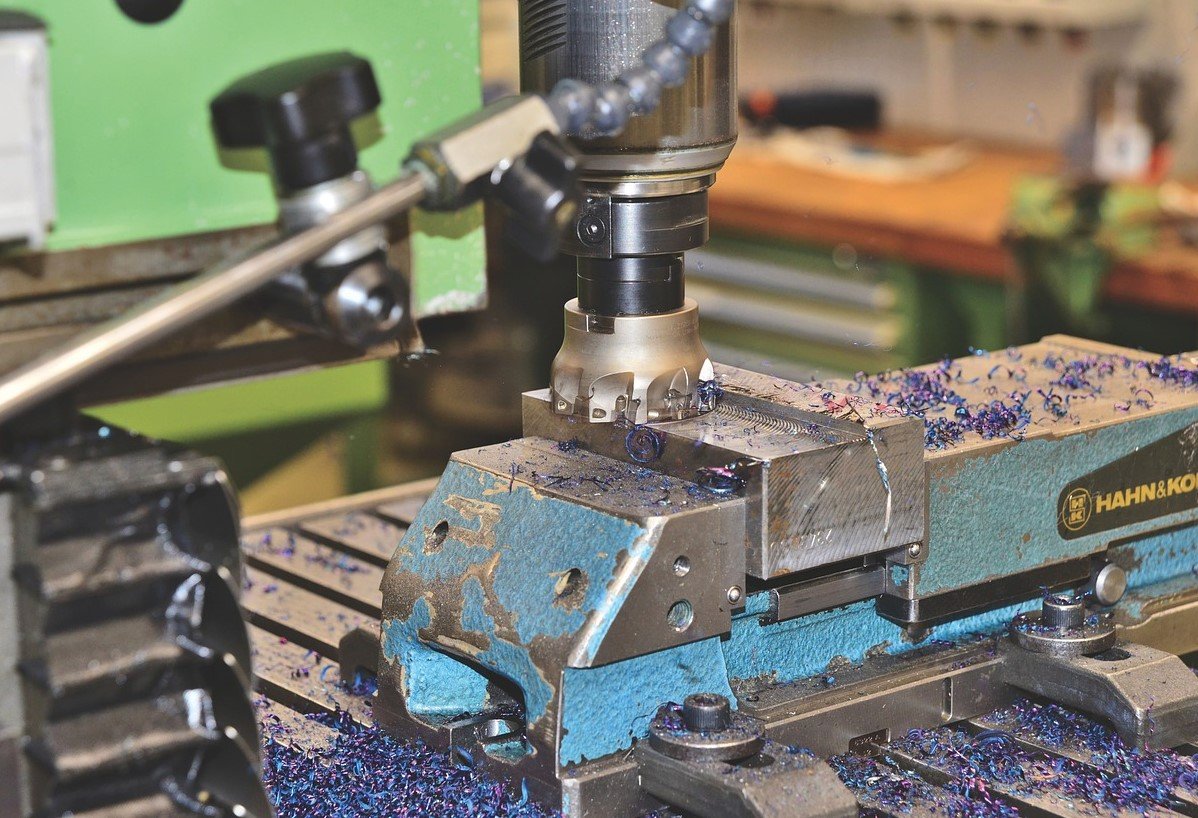
Additive manufacturing, commonly known as 3D printing, has revolutionized the manufacturing industry. It enables the creation of complex components with unprecedented design freedom. Therefore, the 3D printing market is projected to reach $105.99 billion by 2030. According to Fortune Business Insights, it will be growing at a CAGR of 24.9% from 2023-2030.
As the demand for highly customized and intricately designed products continues to surge, precise and efficient additive manufacturing processes become imperative. In this pursuit, laser-based solutions have emerged as the forefront technology, offering unparalleled precision and efficiency in additive manufacturing.
Laser-Based Additive Manufacturing: An Overview
Laser-based additive manufacturing (AM) utilizes high-powered lasers to selectively fuse powdered materials, layer by layer, to build intricate 3D structures. According to Novanta Photonics, laser processing solutions are key to 3D printing. This technology has gained widespread adoption due to its ability to work with various materials, including metals, polymers, ceramics, and composite.
Additive manufacturing offers versatility across different manufacturing applications. It is also useful in minimizing material waste by reducing the materials used in manufacturing the final parts of the product. An ACS Publications study concludes that additive manufacturing has been used to reduce material usage in final parts by 35–80%.
The core principle behind laser-based AM lies in its precision and efficiency. By harnessing the power of lasers, manufacturers can achieve micron-level accuracy and produce complex geometries with minimal material wastage. This level of precision is essential for industries such as aerospace, automotive, and healthcare, where components must meet stringent quality standards.
Advancements in Laser Technology
The evolution of laser technology has played a pivotal role in enhancing the precision and efficiency of additive manufacturing processes. Today, manufacturers have access to various laser sources, including fiber, diode, and CO2 lasers, each offering unique capabilities suited to specific applications.
Fiber lasers, characterized by their high energy efficiency and beam quality, have become the preferred choice for metal additive manufacturing. This is due to their ability to deliver precise and consistent results. These lasers enable rapid heating and melting of metal powders, facilitating faster build rates and shorter production cycles.
On the other hand, diode lasers offer enhanced flexibility and affordability, making them well-suited for polymer-based additive manufacturing processes. With advancements in diode laser technology, manufacturers can achieve finer feature resolution and improved surface finish. This opens up new possibilities for functional prototyping and end-use part production.
Integrating CO2 lasers has further expanded the capabilities of additive manufacturing systems, particularly in ceramics and composites. CO2 lasers provide excellent beam control and heat absorption, enabling precise material deposition and sintering across a wide range of substrate materials.
It is thanks to such recent advancements in laser processing solutions that 3D manufacturing has received strong adoption. Furthermore, advancements in laser scanning technology have improved the accuracy of 3D printing by providing real-time feedback on the printing process. Laser scanners can detect and correct errors as they occur, resulting in higher-quality prints and reducing the need for post-processing.
Moreover, advancements in laser materials processing have expanded the range of applications for 3D printing. Laser ablation, for example, enables the precise removal of material layers, facilitating the creation of intricate structures with high surface quality.
Applications Across Industries
The precision and efficiency offered by laser-based additive manufacturing have unlocked a myriad of applications across diverse industries:
Aerospace
In the aerospace sector, where lightweight yet robust components are critical, laser-based AM enables the production of complex geometries with optimized structural integrity. It allows manufacturers to design components tailored to their specific performance requirements, from turbine blades to structural brackets.
Another key advantage of 3D manufacturing in aerospace is the ability to prototype and iterate designs rapidly. Engineers can quickly produce physical prototypes of new components or modifications, enabling faster design validation and iteration cycles. This iterative approach accelerates the development timeline, allowing aerospace companies to bring new products to market more efficiently.
The aerospace sector is among the biggest users of additive manufacturing. Automation is the only other industry that uses 3D manufacturing as much as aerospace. According to a ScienceDirect study, almost 33 % of the AM revenue is received from aerospace and automotive.
Automotive
One significant application of 3D manufacturing in the automotive industry is prototyping. Automakers can quickly produce prototypes of new vehicle designs or components using 3D printing technology. This allows for rapid iteration and refinement of designs without the need for expensive and time-consuming traditional manufacturing processes.
Additionally, 3D printing enables the production of complex geometries that would be difficult or impossible to achieve using conventional manufacturing methods. This flexibility in design allows automakers to create lighter, more efficient components while maintaining or improving strength and durability.
Another emerging application of 3D printing in automotive is the production of end-use parts. The technology is still evolving in this area. However, 3D printing promises decentralized manufacturing, where parts can be produced on-site or on-demand, reducing inventory costs and lead times for spare parts.
Healthcare
One of the most significant benefits is the ability to create patient-specific medical devices and implants. Using 3D printing technology, healthcare professionals can design and produce implants that precisely match the anatomical structure of individual patients.
Customized prosthetics are another area where 3D manufacturing has made a significant impact. Traditional prosthetics are often generic and may not fit comfortably or function optimally for every patient. With 3D printing, prosthetic limbs can be customized to fit the unique size and shape of the patient’s residual limb. This helps improve comfort, functionality, and overall quality of life.
Dental applications of 3D manufacturing have also become increasingly common. Dentists can use 3D printing technology to create crowns, bridges, and dental implants tailored to each patient’s mouth. This level of customization ensures a better fit and appearance than traditional fabrication methods.
Energy
In wind energy, 3D printing allows for fabricating turbine blades with intricate shapes and structures that improve aerodynamics and energy capture. These blades can be customized based on site-specific wind conditions, resulting in higher energy yields and lower operational costs. According to oilprice.com, 3D printing has streamlined operations in wind energy while providing a high ROI within six months.
Solar energy also benefits from 3D manufacturing techniques, particularly in producing photovoltaic (PV) cells and modules. Additive manufacturing enables the creation of lightweight, durable, and flexible solar panels that can be integrated into various surfaces. Additionally, researchers are exploring 3D printing to develop advanced solar materials with enhanced light absorption and conversion properties.
Challenges and Future Outlook
Despite its numerous benefits, laser-based additive manufacturing still faces challenges that hinder its widespread adoption. These include high equipment costs, limited material options, and post-processing requirements. However, ongoing research and development efforts are focused on addressing these challenges and further optimizing the additive manufacturing process.
Looking ahead, the future of laser-based additive manufacturing holds immense promise. As advancements in laser technology improve precision, speed, and material compatibility, the use of additive manufacturing across industries may be further facilitated.
In conclusion, laser-based additive manufacturing represents a transformative technology revolutionizing how we design, prototype, and manufacture products. With its unparalleled precision and efficiency, laser-based solutions offer manufacturers the flexibility to create complex geometries and customized components with unprecedented accuracy. Laser-based additive manufacturing will play an increasingly integral role in driving innovation and competitiveness across various industries.
-
Entertainment2 months ago
Bflix.gg Not Working? Here’s Where You Can Stream Free Now
-
Fashion2 months ago
Vintage Styles Making a Comeback: Trends You Should Know
-
Tech1 month ago
Latest Durostech Updates: Key Highlights
-
Entertainment2 months ago
Is Shannon Reardon the Same as Swanick? Here’s What We Know