Business
Breaking Down the Plastic Vacuum Forming Process
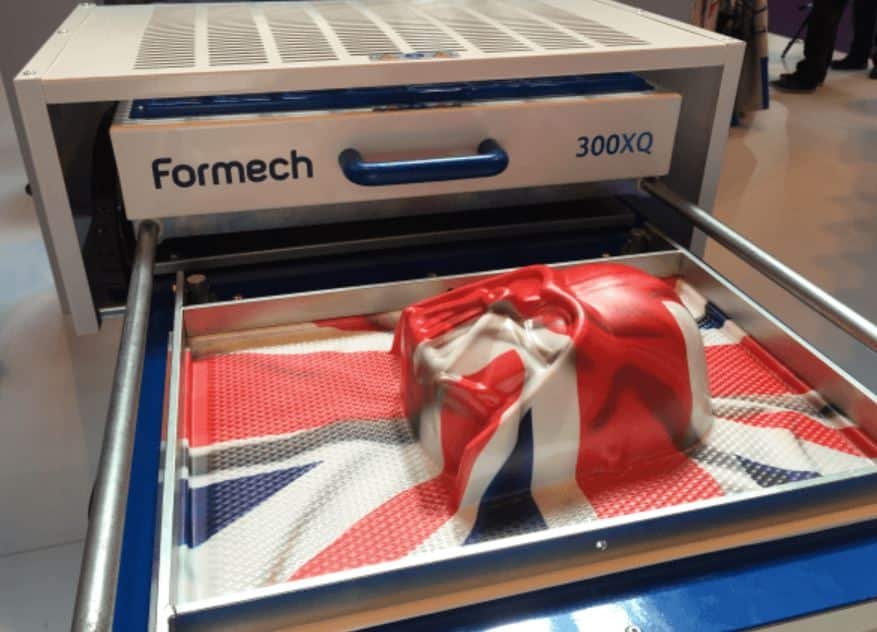
[lwptoc]
What Is Vacuum Forming?
Vacuum framing is an assembling technique used by plastic manufacturers to shape plastic materials. During the vacuum shaping cycle, a sheet of plastic is warmed and afterward pulled around a solitary form utilizing attractions.
Vacuum shaping is utilized for a wide scope of assembling applications, going from little custom parts created on work area gadgets to enormous parts produced on robotized modern apparatus.
What are the Differences Between Vacuum Forming, Thermoforming, and Pressure Forming?
Thermoforming is an assembling cycle where a sheet of plastic is warmed to become flexible, then, at that point, formed or shaped utilizing a form, and managed to make a last part or item. Vacuum framing and strain shaping are both various sorts of thermoforming measures. The principal contrast between pressure framing and vacuum shaping is the number of molds that are utilized.
Vacuum shaping is the most straightforward type of plastic thermoforming that utilizes one form and vacuum strain to get the ideal part calculation. It is great for parts that should be exactly shaped on one side, like molded bundling for food or hardware.
There are two fundamental sorts of molds—male or positive, which are arched, and female or negative, which are inward. With male forms, the sheet of plastic is put over the shape to form within measurements of the plastic part. With a female shape, the thermoplastic sheet is put inside the shape to frame the external components of the part exactly.
In pressure shaping, a warmed sheet of plastic is squeezed (subsequently the name) between two forms as opposed to being maneuvered into place around a solitary shape utilizing pull. Tension framing is great for assembling plastic parts or pieces that should be all the more unequivocally formed on the two sides or potentially require a more profound draw (they need to expand farther/more profound into a shape, for example, apparatus housings that need to look stylishly satisfying on the outside and fit properly or fit an exact size on the inside side).
-
How Does Vacuum Forming Work?
The bit-by-bit vacuum shaping interaction fills in as follows:
- Brace: A sheet of plastic is set in an open edge and cinched into place.
- Hotness: The plastic sheet is relaxed utilizing a hotness source until it comes to the fitting shaping temperature and becomes flexible.
- Vacuum: The system containing the warmed, malleable sheet of plastic is brought down over a shape and maneuvered into place through a vacuum on the opposite side of the form. Female (or raised) molds need to have minuscule openings bored into holes with the goal that the vacuum can successfully maneuver the thermoplastic sheet into a suitable structure.
- Cool: Once the plastic has been conformed to/into the shape, it needs to cool. For bigger parts, fans or potentially cool fog are at times used to accelerate this progression in the creation cycle.
- Delivery: After the plastic has cooled, it tends to be taken out from the form and let out of the structure.
- Trim: The finished plastic part should be removed from the abundance material, and edges should be managed, sanded, or smoothed.
Vacuum framing is a moderately fast cycle with the warming and vacuuming steps normally requiring a couple of moments. In any case, contingent upon the size and complexity of the parts being made, cooling, managing, and making molds can take significantly more.
The advantages and disadvantages of Vacuum Forming
Numerous makers, creators, and different experts pick vacuum shaping since it offers a mix of plan adaptability for a moderately minimal price contrasted with other assembling techniques. The advantages of vacuum shaping include:
-
Moderateness
Especially for more modest creation runs (250-300 units each year), vacuum shaping is commonly more reasonable than other assembling techniques, for example, plastic infusion forming. The reasonableness of vacuum shaping is to a great extent because of the lower cost for tooling and plastic rapid prototyping. Contingent upon the surface space of the parts being fabricated and the components of the cinch outline, tooling for infusion embellishment can cost a few times more than the sum for tooling for plastic thermoforming or vacuum shaping.
-
Turnaround Time
Vacuum shaping has a quicker turnaround time than other conventional assembling techniques on the grounds that tooling can be made quicker. Creation time for vacuum shaping tooling is commonly half as long as the measure of time needed to deliver tooling for infusion forming. At the point when 3D printers are utilized to make molds, turnaround time can be significantly quicker. By expanding creation measure productivity, vacuum shaping empowers organizations to get new plans in the possession of customers quicker.
-
Adaptability
Vacuum shaping gives creators and makers’ the adaptability to try out new plans and fabricate plastic designs without the monstrous overhead or slack occasions. Molds can be made out of wood, aluminum, underlying froth, or 3D printed plastics, so they can be changed out as well as adjusted all the more handily contrasted with other assembling measures.
Dick Teal utilized vacuum shaping to try out models of John Deere snowmobile parts in the last part of the 1970s and mid-’80s, to a great extent since it made tooling reasonable. In the book, John Deere Snowmobiles: Development, Production, Competition and Evolution, 1971-1983, the writers clarify that “a mutually beneficial arrangement was made with cheaper parts and less interest in assembling tooling.”
Check out: How to Take Your Manufacturing Business to the Next Level