Business
Sand Control Methods For Oil Extraction Companies
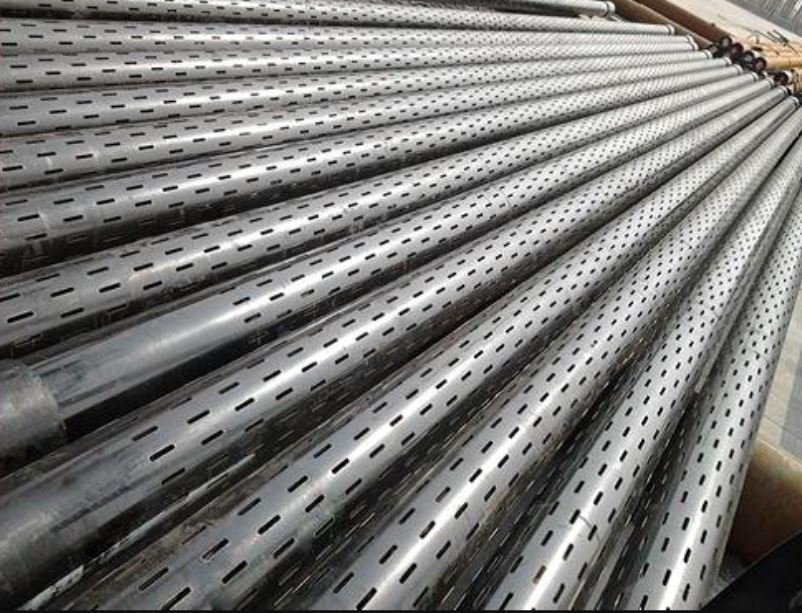
When the oil is recovered from the natural reservoirs, it comes with many impurities, and sand is one of them. As an impurity, the amount of sand present in the collected oil must be eliminated or controlled at the lowest amount.
This is where the sand control methods come to action. If you are dealing with oil recovery, you might know how important it is to opt for sand control methods. Here in this article, we will talk about different sand control methods and their equipment.
[lwptoc]
What Is A Sand Control Method?
Let’s start the discussion with a typical definition of sand control methods. The name itself suggests that a sand control method is all about controlling the sand production into a wellbore.
Sand production can lead to various issues; they are as follows.
- Production impairment due to sand plugging.
- Damage surface facilities piping, separator, etc.,
- Erosion to the completion string along with the downhole tool.
Available Sand Control Methods
After getting the basic idea of the sand control method, it is time to know the different types of available sand control methods. There are basically two types of sand control methods. They are active sand control and passive sand control.
Active Sand Control
To control sand production, active sand control always relies on the usage of filters, and it is basically known as an intrusive measure. The following are the active sand control methods.
- Chemical consolidation.
- Gravel pack & Frack Pack.
- Expandable sand screen.
- Stand-alone screens.
Passive Sand Control
After active sand control, the passive sand control method utilizes non-intrusive measures to mitigate, control, or avoid sand production. Here are the passive sand control methods.
- Sand management.
- Selective perforation.
- Oriented perforation.
Top Sand Control Methods
We understand how much you want to know the details about the sand control methods. That is why we have curated some of the most popular and used sand control methods for oil extraction companies.
Wire-Wrapped Screen
We are starting the discussion with a briefing of wire wrap screens. With a wire-wrapped jacket welded around, wire wrapped screen is basically a perforated pipe. The wires that are enclosed in the vertical ribs have the shape of a keystone.
They are designed in order to mitigate the risks of sand plugging the screen. In addition, it becomes more efficient, as it has a self-cleaning action. There are three main types of wire-wrap screens, which are listed below.
- Pipe-based slip-on.
- Rod-based screens.
- Pipe-based direct build screens.
Slotted Liner
One of the oldest sand control methods is slotted linear. It is all about tubing with a series of slots cut through a tubular wall in a specific axial orientation. Across the slots, for creating interparticle bridging, the width of slots is designed.
Apart from being very simple, at the same time, it is also the least expensive way of crafting a standalone. Here are some of the measures that might help you.
- The average flow area is around 3%.
- But on the contrary, it also can go up to 6% of the total pipe area.
- Though, the flow areas of more than 6% would be detrimental to the tensile strength of the pipe.
Expandable Sand Screen
Do you want to know what the latest screen technology is? Yes, an expandable sand screen it is. An expandable screen includes the following four main parts.
- Filtration media.
- Integral expandable connector.
- Base pipe.
- Outer protection shroud.
Here we are also helping you with some of the critical benefits of expandable screens compared to formation.
- Offers a high inflow area.
- Provides maximum hole diameter.
- Gives wellbore support.
- Effective sand control.
Pre-Packed Screen
It is pretty similar to wire-wrapped screens; the filtering media is different here. Here, a media gravel layer is positioned around the internal screen component both with or without a resin coating. The external screen is there to support it.
Based on the requirements of the specific well, the size and thickness of the medium layer differ. When we are saying the requirements, we are referring to the following things.
- Hole size.
- Flow rate.
- Formation size etc.
Final Thoughts
We hope the above pieces of information are enough to offer you the solution you were searching for. However, in case you have any further queries or doubts, feel free to get in touch with us. We will always come up with a reliable and straightforward solution.
Read more: Astor Asset Management Partners with Saudi Arabian Company in a Solar Super Deal
-
Entertainment2 months ago
Bflix.gg Not Working? Here’s Where You Can Stream Free Now
-
Fashion2 months ago
Vintage Styles Making a Comeback: Trends You Should Know
-
Tech1 month ago
Latest Durostech Updates: Key Highlights
-
Entertainment2 months ago
Is Shannon Reardon the Same as Swanick? Here’s What We Know